TKL Company Profile
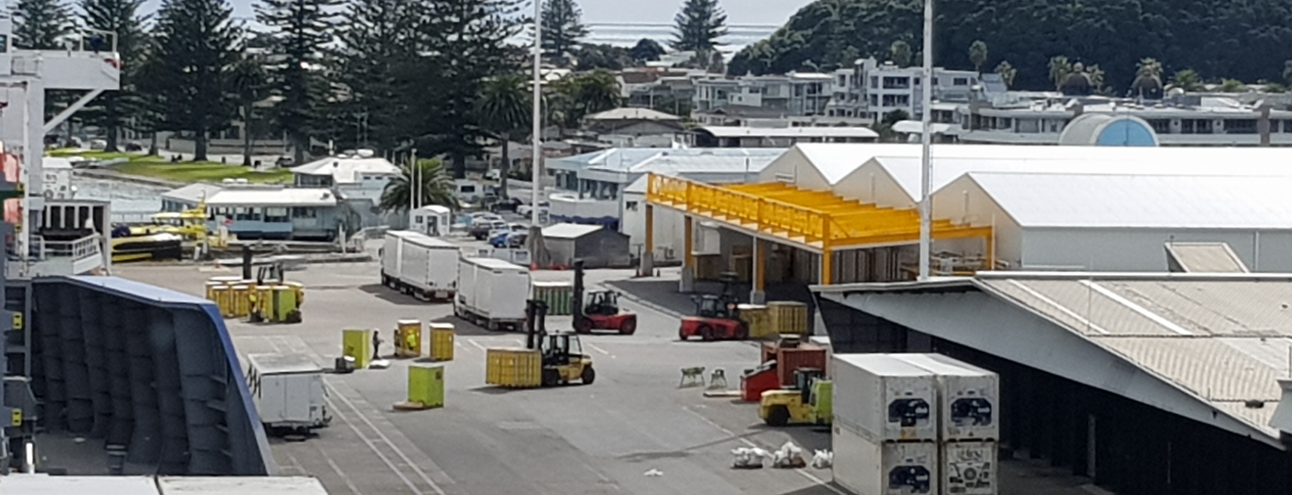
“PROVIDING LEADING EDGE LOGISTICS SOLUTIONS TO THE NEW ZEALAND KIWIFRUIT INDUSTRY”
Welcome to TKL Logistics were everyone has the right to go home to their families and friends every night safe and without injury.
TKL Logistics Limited or “TKL” as it is most commonly known is a company that evolved from a joint venture partnership established in 1999 after phase three of the government and grower led Kiwifruit Industry review process.
Prior to the 2000 export season the joint venture partners formalized the arrangement into a registered company under the name of Tauranga Kiwifruit Logistics Limited. This trading name was in use until the end of 2016 where it was then shortened to TKL Logistics Ltd
The five founding members of TKL were Southlink, G6 Kiwi, Satara, Seeka Kiwifruit Industry’s and CMS Logistics.
In 2006 CMS Logistics joined G6 and relinquished their shares proportionally to the other shareholders
The business has continued on the basis that all shareholders have equal shares and equal voting rights, (not industry share)
SERVICES.
Road Transport
The starting point for TKL involvement in its customers business is the collection of export Kiwifruit from their sites, this is by using either curtainsider or specialised container trucks and in 2018 TKL will manage the transportation of some 28,000 loads of export Kiwifruit.
Transport operations are undertaken in Northland, Auckland, Waikato, Bay of Plenty Nelson and Motueka.
TKL contracts nationally 60 specialist container units and 50 curtainsider’s. The number of trucks engaged on a given day will however vary according to demand.
The transport of Kiwifruit is coordinated by three specialist transport coordinators using custom built software which is integrated into suppliers / coolstores inventory management systems.
The coordination system is continually being refined to assist with TKL’s customers’ requirements and a new mobile application will be implemented shorty which will ultimately provide real time tracking of trucks and provide more up to date information to loadout sites. This system will also allow us to manage the travel of product through specific areas if required as was case during a pest incursion incident a number of seasons ago. The application also has a Health and Safety integration link were upon being sent a job the driver will also be given a list of the specific risks for that loadout site, it will also pre-determine the pickup order of combined loads so that right turns across lanes of traffic will be minimized for obvious safety reasons.
On Wharf Cool storage
At the Mount Maunganui wharf TKL operates a 5200-pallet buffer store to both facilitate the loading of specialised reefer vessels and consolidation of cargo for container loading.
Specialised reefer vessels are able to load 24 hours a day and 7 days a week so the coolstore is integral to this with cargo being preloaded into the store prior to the vessels arrival which allows the loading through the night.
The coolstore also has a direct impact on our charter road transport rates, (with quick turn times truck utilization is up and rates reflect this).
Stevedoring
TKL contracts a stevedoring company to load specialised charter vessels. Ships in Tauranga are loaded on 24 hours a day, 7 days a week basis. The intension is to fully load a vessel in 24 hours. The only constraint to this is intended to be the weather.
Stevedoring a vessel in Tauranga normally involves four gangs of six people working the ship with a marshaling forklift feeding cargo to each gang.
Port Company’s and their charges
Port Company’s and the services they provide to the industry are an integral part of the pre-FOBS logistics process. In Tauranga TKL and Zespri have a 10-year joint services contract with the Port of Tauranga, which covers port usage charges, and a container volume recognition scheme.
The relationship between TKL and the Port of Tauranga has seen the establishment of a dedicated Kiwifruit container truck exchange site at Sulphur Point, this has separated Kiwifruit operations from all other users of the terminal, this immediately resulted in a 20% increase in our transport fleets utilization. It is seen as a critical development in the ability to handle the industry’s growth strategy in the coming years.
Administrative services.
In 2009 efficiencies were realized through the implementation of an industry wide centralized accounts system. The system has automated the way receivables and payables are dealt this.
All accounting transactions are now systemised using buyer created invoicing. Service providers are sent an electronic file detailing the work they have completed for TKL and customers receive the contra charges again in an electronic file format. Customers then have the ability to validate the charges by importing the file into their own inventory systems.
The entire industry volume is now administered now by one person.
Zespri Services
Since 2006 TKL has had a contract with Zespri to provide professional services relating to the loading of ships.
These services include.
-
Vessel stowage planning. (planning which cargo goes were on the vessel)
-
Cargo superintendant services (Checking industry best practice principles are used to load vessels)
-
Data capture (Record electronically all pallets arriving on the wharf and allocating them to an area on the ship)
-
Vessel reconciliations. (Provide a reconciled account of what pallets are loaded on an individual vessel)
-
Provide Plant, Equipment and Buildings for the ECPI (Export consignment Product Inspection) process.
With TKL managing all on wharf functions this has provided efficiencies to the industry (people and financial).
REVENUE
Apart from the Services agreement TKL has will Zespri all charges are received and paid for on behalf of Grower Entities or Post Harvest companies.
The company operates on a cost only basis for the services it provides and adds no margin to Transport, Stevedoring or Port charges, the cost of administering the business is via a minimal administration charge on all cargo handled ($0.003 cents per tray)
The company also has an agreement with Zespri which rebates money back to TKL if Chartered Reefer ships are processed through the port efficiently.
Our third area of income is the annual contract with Zespri for provision of the services previously mentioned.
MANAGEMENT OF SURPLUS INCOME
TKL neither pays profits or dividends to its shareholders.
Surplus funds at the end of each season are rebated back to its customers. These rebates are calculated based on the number of pallets supplied by customer in a season through the TKL operation, for example if an entity supplies 10% of all pallets they receive 10% of the total rebate.
THE PEOPLE
The company has a team which looks after the day to day running of the business.
-
- Ian Mearns Chief Executive
- Tory Oliver Company Administrator
- David Burt Operations Manager
- Ricky Child Port Operations Manager
- Teressa Hamill Charter Checkpoint operator
- Debbie Beange Charter Checkpoint operator
- Brendon Keenleyside Checkpoint operator and Container Logistics
- Emily Adamson Container Checkpoint operator
- Daisee Killen Container Transport and Logistics Coordinator
- Joanne Scott Container Transport Coordinator
- Jeremy Baker Charter Transport Coordinator
- Richard Hayward Cargo planning
- Ian Mearns Chief Executive
TKL Board of Directors,
-
Stephen Butler G6 Kiwi Logistics Ltd
-
Hamish Simson Eastpack Ltd
-
Michael Franks Seeka Ltd
HEALTH AND SAFETY
The TKL Directors, management and staff are committed to providing a Healthy and Safe working environment for all and we accept that this commitment is everyone’s responsibility.
An important component of our Health and Safety systems is the recognition of the multiple PCBU’s working together, on any day there may be as many at 18 PCBU’s working on TKL’s sites.
To assist with our zero-harm target TKL has a specialist external resource which manages our systems and auditing via the recognized “SAFE 365” program.
In addition to our internal participation meetings there is a wider site Health and Safety committee which is made up of staff from TKL Logistics, ISO Limited and Zespri International.
FUTURE PLANNING
TKL is fortunate to be part of a growth industry and has therefore been working on a strategy to increase its capacity since 2015.
A significant part of this strategy was the development of a new port coolstore on the Mount Maunganui wharf which was completed in time for the start of the 2018 Kiwifruit season.
It was also recognized that proportionally more volume would be export in containers hence a need to build out container capacity. In 2015 in the Bay of Plenty transport fleet consisted of 20 trucks and has been steadily grown to 47, 29 tonne capable units in 2018. With the growth has come the capacity to be able to handle 200 containers a day or 1000 per week.
TKL is also recognising that transport is changing and is now evolving to the use of new high productivity transport configurations, curtainsider’s units can now be capable of transporting 28 pallets instead of the previous 24 and Container trucks now have increase weight limits buy the introduction of more axles and longer overall length. It is hoped that within the next couple of years we will increase container weight limits to 30 tonne (currently 29) which will provide Zespri with sea freight efficiencies.
The one constraint that all of the Kiwifruit industry is facing is the shortage of labour and TKL is actively developing strategies to deal with the demand for a seasonal work force on the port. Part of this strategy will be to make sure companies contracted to TKL have a plan to attract workers to the business and relying on people simply walking up in April to start work is work is not an acceptable plan.